what type of welding is used for sheet metal Sheet metal welding is a welding process used to join thin metal sheets, usually involving metal materials with a thickness of 1/16 inch (about 1.5 mm) to 1/4 inch (about 6 mm). The process is commonly used for different types of metals, such as aluminum, stainless steel, and carbon steel, and is widely used in manufacturing, construction . Selecting the Right Enclosure Using NEMA and NFPA 70. Choosing the right electrical enclosure involves understanding both NEMA ratings and NFPA 70 classifications. Here’s a step-by-step guide: 1. Identify the Environment. Determine whether the environment is indoor or outdoor. Assess the presence of dust, water, corrosive elements, or other .A junction box provides a code-approved place to house wire connections, whether for outlets, switches, or splices. Here's how to install one.
0 · welding sheet metal with mig
1 · welding 24 gauge sheet metal
2 · welding 22 gauge sheet metal
3 · welding 20 gauge sheet metal
4 · welding 14 gauge sheet metal
5 · tig welding thin sheet metal
6 · tig welding stainless sheet metal
7 · mig welding sheet metal basics
Designed for outdoor use, NEMA enclosures protect electronics exposed to severe weather. Types like NEMA 3, 4 and 4X secure equipment against rain, snow, ice, windborne debris and temperature extremes.
Each welding process requires specific precautions and equipment setup for a successful sheet metal weld. So, let’s discuss the preparation needed for each arc welding process before proceeding to the common problems with thin gauge welds. See moreNow that we’ve covered the essential considerations for different arc welding processes, let’s discuss how to prevent and fix common . See moreWelding thin metal is challenging. There is no denying that. But, if you practice and use the tips we shared in this article, you’ll get the best chance for success. After you inevitably burn through some scrap sheets of metal and warp others, you’ll gain more experience and learn . See more 6 Methods of Sheet Metal Welding. Now, let’s take a comprehensive look at some methods for melding metal sheets. 1. MIG Welding. Metal Inert Gas welding (MIG), also known as Gas Metal Arc Welding. It .
Sheet metal welding is a welding process used to join thin metal sheets, usually involving metal materials with a thickness of 1/16 inch (about 1.5 mm) to 1/4 inch (about 6 mm). The process is commonly used for different types of metals, such as aluminum, stainless steel, and carbon steel, and is widely used in manufacturing, construction . Learn about the techniques used in sheet metal fabrication and the different types of welding, along with safety measures to consider. Manufacturer of Metal Working Machinery 1-800-391-5419
With these materials, use a tri-mix gas — 90% helium, 8% argon and 2% CO2. To weld sheet metal with solid wires, use electrode positive (EP, or reverse polarity). Don’t attempt to weld thin materials like sheet metal with flux . Utilize filler metals (wires) that are slimmer as compared to reedy sheet metal. Numerous welders utilize 0.023-inch diameter wires and 0.024 inches for slimmer sheet metals. 18-gauge metals such as stainless steel have wire diameters of 0.030 and 0.034 inches. . Not every one of us begins welding each metal type flawlessly every time . For thin sheet metal welding it can be 30 ampere while for thicker (e.g. 1/8” square groove weld)- it can go up to 220 ampere for example. GMAW-S gives low heat and makes it easy to use in all positions on sheet metal, low carbon steel, low alloy steel, and stainless steel sheet metal from 25 gauge (0.02 inch or 0.5 mm) to 12 gauge (0.1 inches or 2.6 mm). Welding sheet metal is a critical component of metal fabrication. The welding technique is used to join metal components. There are a significant number of distinct types of welding, which is one of the most prevalent techniques for joining metal objects.
3. Adjust Your Torch Angle. Changing the torch angle when MIG welding goes a long way to preventing burn-throughs. Make sure you adjust the angle to shorten the distance between the tip and the metal, no matter the welding position you work in.This will make the arc more stable, giving you more control over the weld and lessening the chance of burn-through. Essential Tips on How to Weld Auto Body Sheet Metal Use the skip welding technique. Using a skip welding technique will help prevent heat build-up and warping. Skip welding consists of laying a series of tack welds about an inch apart and joining them together in a different order instead of one long bead. These short welds at different points . Induction welding; Welding Sheet Metal. For welding purposes, the term “sheet metal” is restricted to thicknesses of metals up to and including 1/8 in. (3.2 mm). Welds in sheet metal up to 1/16 in. (1.6 mm) thick can be made satisfactorily by flanging the edges at the joint. The flanges must be at least equal to the thickness of the metal. Laser welding is a cutting-edge production technique that utilizes a laser with high energy density as the heat source for welding. It is widely used in the sheet metal manufacturing industry due to its advantages, including high energy density, fast welding speed, environmental friendliness, minimal plate deformation, and more.
The world of sheet metal fabrication is hardly one-size-fits-all. This article aims to break down some of the important differences between common metals; however, it should be noted that the below descriptions are subject to variation based on different alloys and grades of the material.
welding sheet metal with mig

welding 24 gauge sheet metal
Welding nearly always causes some distortion: the metal in and around the weld shrinks as it cools, and this shrinking often upsets the shape of the metal. Sheet metal is particularly sensitive to this type of distortion (often called warping) but there are ways to mitigate this characteristic, which we will detail here. Metal Types used in Sheet Metal Welding. After discussing the welding methods, it is important to know about the common metal types used nowadays. Let’s find out the Advantages of Metal Welding as each metal possesses its unique properties and utility. Table: Metals used for sheet welding, their properties and applications

Typically, you can weld sheet metal as thin as 0.5mm (around 0.02 inches) with processes like MIG or TIG welding. However, welding thin sheet metal requires precision and skill to prevent burn-through and warping. Can I use a regular welding machine for sheet metal? Yes, you can use a regular welding machine for sheet metal.
Sheet Metal for Laser Welding. Not all types of sheet metal are suitable for laser welding. The material properties and thickness of material play a crucial role in determining the weldability of thin sheet metal. The welding . You can weld a 22-gauge (0.03-inches) metal sheet using a TIG welder or even with a MIG welding unit. However, it is not recommended to stick weld 22-gauge sheet metal as excessive penetration is highly likely to occur . When selecting the optimal welding joint type for a sheet metal project, several crucial factors must be taken into account to guarantee strength, durability, and efficiency. The type and thickness of materials, specific .
Both sheet metal welding and sheet metal soldering are common activities, yet require utmost care while performing in order to achieve accurate end results. The decision to choose amongst the two should be based on the application requirements, strength requirements and type of metal used, among others. Stick welding, also known as Shielded Metal Arc Welding (SMAW), is a basic welding method where you use a flux-coated electrode and an electric current to produce the weld. It is suitable for thicker sheet metal made of steel or stainless steel but less for thin sheets due to higher heat input and less control over penetration.In the case of thinner sheet metal or highly ductile metals (such as aluminum or copper), even more care must be taken in the sheet welding process. How to weld thin sheet metal. Heat is essential when welding thinner material. Minifaber machines can control the amount of heat, welding any sheet below 0.8 mm without any problem. With this type .
Sheet metal welding is a crucial fabrication process because it is one of the simplest ways to join cut-out pieces of metal sheets to create the desired shape. . Type. Welding speed. Materials of sheet. 1. MIG. 20 to 30″ / minute. automated : up to 1oo ″ / minute. Carbon& stainless steel, Aluminum. 2. TIG.Adjust the welder settings according to the thickness of the sheet metal and the type of wire being used. This typically involves setting the voltage and wire speed, which will vary based on the specific project and equipment. . What type of gas should I use for welding sheet metal? A: A mix of Argon and CO2 is commonly used for its . These two types of welding comprise what is known as Gas Metal Arc Welding (GMAW). Both forms use a shielding gas and a metal wire fed through the welding gun (like a glue gun). In MIG (Metal Inert Gas) and MAG (Metal Active Gas) welding, an electrical arc is generated between the base metal and an electrode on the tip of the gun, a gas is .
The welding of thin sheet metal is an issue that most beginners in the art will encounter at one point in time or the other. Shielded metal arc welding (SMAW), commonly referred to as stick welding, is one of the welding processes that is applicable to thin materials as long as the right procedures and equipment are used. The best welding method for sheet metal depends on metal type, thickness, joint configurations, surface orientation, and fabrication requirements. However, TIG is the most appropriate when welding thin metals because of its precise hag control and versatility, offering you a satisfactory weld. Learn about some common sheet metal forming processes and their unique qualities. 5 Common Types of Metal for Welding. The following types of metal are commonly used for welding: 1. Aluminum. Aluminum is one of the most popular materials for welding due to its light weight, strong corrosion resistance, and high conductivity.The four main processes for forming sheet metal are bending, rolling, stamping, and spinning. Each process provides its own unique advantage, depending on the specifics of the sheet metal being formed. At JWK Engineering & Sales, we provide a range of sheet metal forming services using different sheet metal fabrication tools and equipment.

welding 22 gauge sheet metal
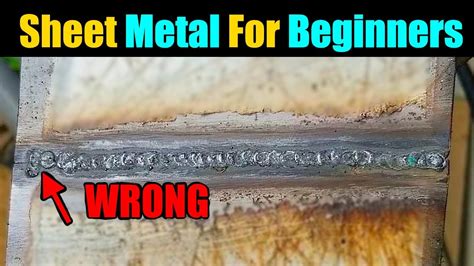
small metal house letters
12-in D x 18-in W x 39-in H 4 tier white powder coating wire shelving unit 12x18x39in. Strong steel construction with durable white finish. Standard 1-inch (25mm) shelf adjustment. Easy to assemble with no tools required. Each shelf can support a weight capacity of up to110lbs (on leveling feet) Total max load weight with leveling feet is 440lbs
what type of welding is used for sheet metal|welding 20 gauge sheet metal